コーティング
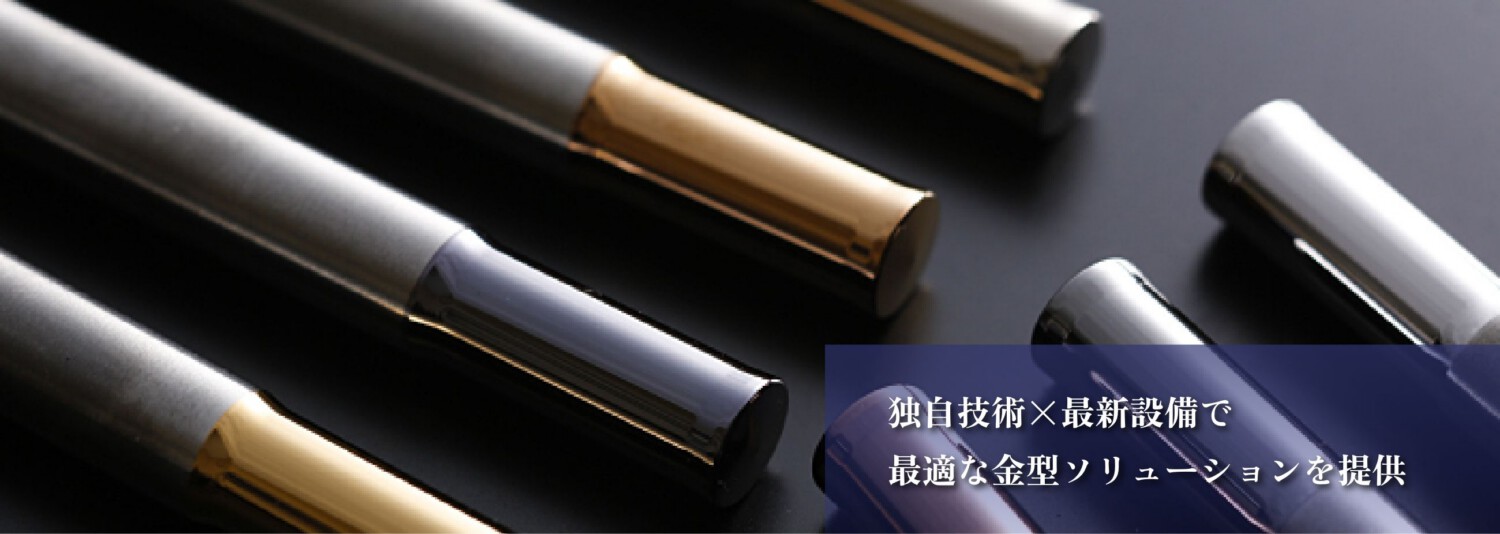
金型製造の短納期化およびPVDコーティングの多様化に伴い、当社では最新のPVDコーティング設備を導入し、2013年よりPVDコーティングを開始致しました。
これまで培った独自のラッピング技術との融合によって、金型の耐久性を向上させます。
徹底した品質管理のもと、各金型要素に最適なオリジナルコーティングをご提案し、金型の耐久性向上にお応え致します。
PVDの原理と成膜手法
PVDとは物理的な成膜方式で、主に高真空(10-1〜10-5Pa)の状態において、皮膜となる成膜物質を加熱、スパッタリング、電子ビーム、ホロカソード、レーザー、アーク放電などで粒子(原子・分子・イオン等)の状態に蒸発・飛散させ、基材表面に付着・堆積させる方法です。 金型へのPVDでは電子ビーム、ホロカソード、アーク放電による手法が広く実用化されております。電子ビームやホロカソードによる手法は比較的平滑な表面が得られやすいものの、合金化した個体原料による成膜ができないことから、アーク放電による手法が広く実用化されております。
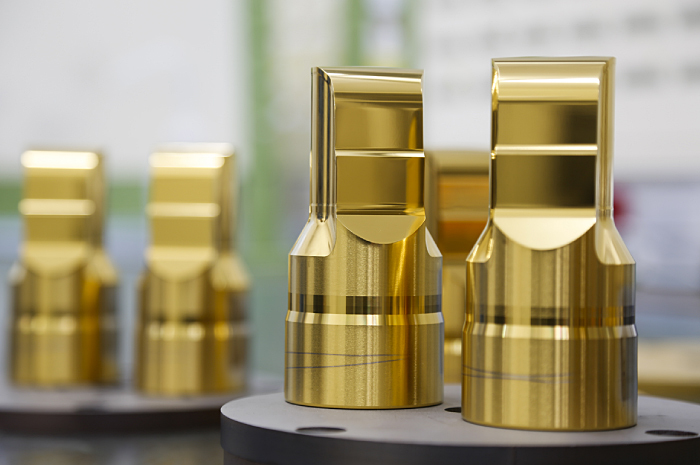
当社ではPVDの中でも成膜時のエネルギーが高く密着強度に優れる改良型アーク放電式イオンプレーティングを採用しております。
通常アーク放電式イオンプレーティングではドロップレットと呼ばれる金属粒子が不可避的に皮膜に混入します(図1)。このドロップレットは面粗度を劣化させ、使用時のカジリや焼付きの起点となることから、コーティング後の磨きによって凸部を除去し平滑化することが一般的です。しかしながら凸部を除去しても粒子状のドロップレットが脱落した後は凹部となり、凹部も同様に異常摩耗の起点となる場合があるため、ドロップレットそのものを低減することが必要です。当社では、このドロップレットを効率的に減少させる特殊なアーク蒸発源を採用し、従来のアーク放電式イオンプレーティングよりも平滑な表面を実現しました(図2)。さらに、コーティング後に最適な磨きを加えることで金型表面として最適な表面に仕上げます。
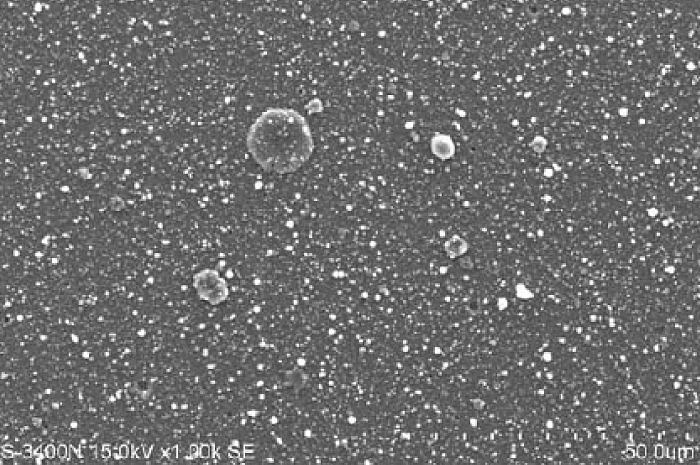
図1:
通常アーク放電式イオンプレーティングによる表面
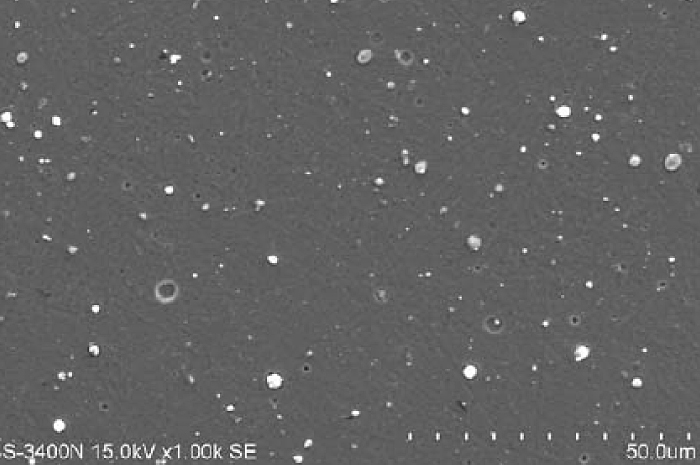
図2:
改良型のアーク放電式イオンプレーティングによる表面
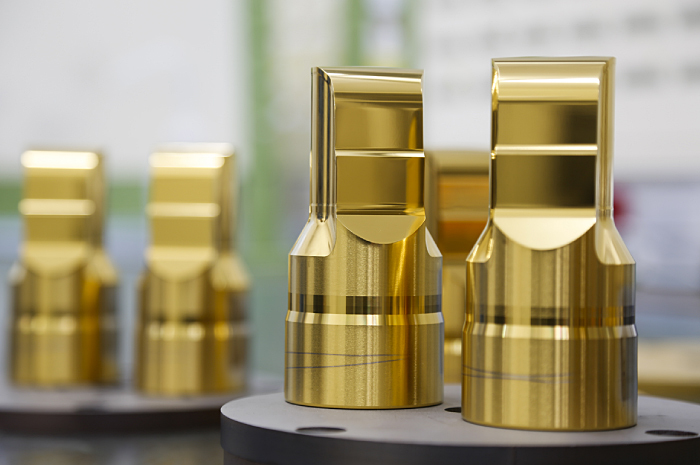
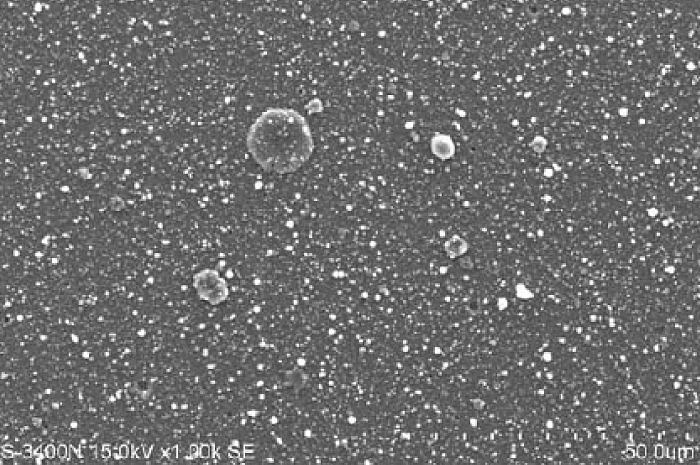
図1:
通常アーク放電式イオンプレーティングによる表面
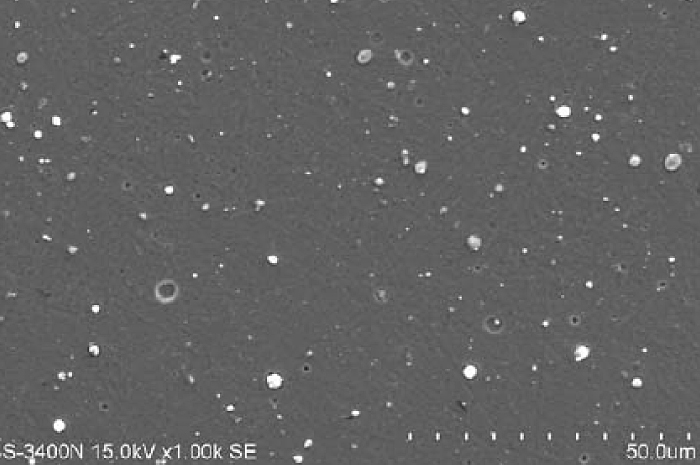
図2:
改良型のアーク放電式イオンプレーティングによる表面
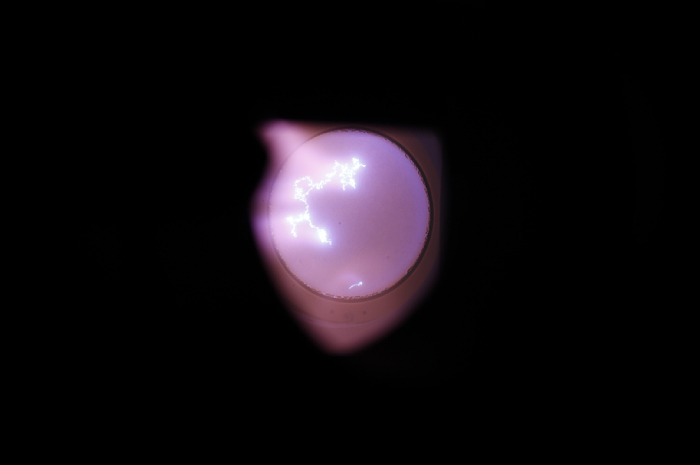
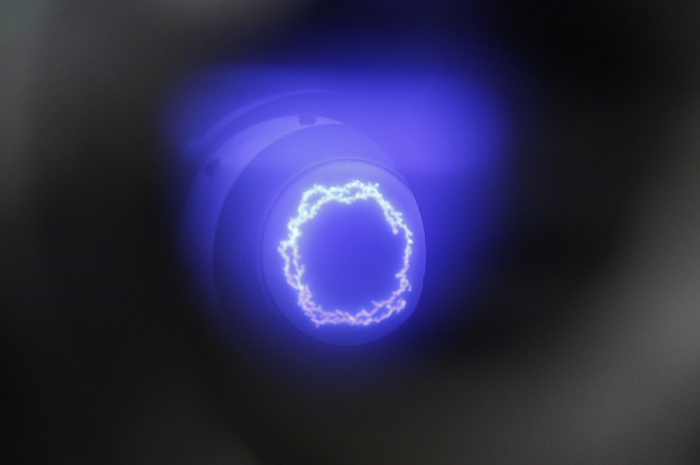
PVDメリット
金型に耐摩耗性や耐焼付き性等を付与するために、金型表面にCVD(化学蒸着法)やPVD(物理蒸着法)により、セラミックス膜をコーティングすることが多用されるようになってきました。特に、最近ではPVDの普及が急速に進んでおります。それは以下の理由によると考えられます。
PVDでは低温(一般的に鋼の焼き戻し温度以下)被覆するため金型基材の変形が少なく(PVDでは0.01㎜以下の寸法精度対応可、CVDでは0.01以下の寸法精度対応不可)、しかもコーティング膜が緻密であり硬度が高くなります。
PVD膜表面には被覆後に圧縮応力が残留することに対し、CVD膜表面では基材とセラミックス膜の熱膨張係数の違いから引張応力が残留します。そのためCVD膜表面にはクラックが生じ易く、このクラックを起点とした異常摩耗がPVDに比べ生じ易くなります。
PVDでは金型形状によって膜厚分布が均一でないため、金型の内径処理の場合は入口付近の膜厚が厚くなる傾向にあり内径処理が困難でした。しかし最近ではPVDでもCVDと同等以上の膜厚を被覆できるようになり、PVDの欠点であったダイス等の内径処理も対応できるようになりつつあります。当社ではコーティング膜厚を予測した磨き(ラップ)によって内径の寸法管理にも対応しております。
PVDは各種金属又はその合金等の個体を原料とすることから、気体を原料とするCVDに比べて成分系の選択肢が広くなります。最近では3成分系以上の窒化物も金型へ適用されるようになってきました。
コーティング特性
各金型要素に最適な各種オリジナルコーティングをご用意しております。
特徴を下表に示します。
選定にお困りの場合は、現在ご使用の金型をお預かりして観察・調査に基づいて、最適な表面処理のご提案をさせて頂きます。
処理 コード |
主成分 | 色調 | 標準膜厚(片肉) 〈μm〉 |
硬度 〈Hv〉 |
耐熱温度 〈℃〉 |
摩擦係数 〈μ〉 |
特徴 | 摩擦耗性 | 表面粗度 |
---|---|---|---|---|---|---|---|---|---|
CRN ![]() |
CrN系 | 白銀 | 4-6 | 1800 | 600 | 0.5 | 靱性が高く安定した特性 | -- | - |
TCN ![]() |
TiN TiCN系 | 黄金 | 3-5 | 2200 | 500 | 0.5 | 汎用性に優れ各種金型への適用実績も豊富 | - | - |
ALM ![]() |
TiAIN系 | 黒紫 | 4-6 | 2800 | 900 | 0.7 | 高耐熱系汎用。バランス型。ダイスへの適用実績も豊富 | + | + |
TSP ![]() |
TiSiN系 | 赤銅 | 3-5 | 3800 | 950 | 0.8 | 高圧縮応力、バランス型。ダイスへの適応実績も豊富。 | ++ | + |
ALC ![]() |
AlCrN系 | 青藍 | 2-4 | 3300 | 1000 | 0.7 | 耐摩耗性に優れる。鉄系、超硬系にも相性良い | +++ | + |
ALZ ![]() |
AlTiCrN | 黒灰 | 4-6 | 3300 | 1000 | 0.7 | 耐摩耗性に優れる。鉄系、超硬系にも相性良 | +++ | + |
MSP-Q ![]() |
AlCrN系 | 黒青 | 2-4 | 3400 | >1000 | 0.6 | ALZよりも面粗度、耐摩耗性に優れる | ++++ | ++ |
MSD ![]() |
DLC系 (ta-C) | 虹 | <1 | >6000 | 400 | 0.1 | 水素フリーDLC、非鉄材加工で耐摩耗、耐凝着性に優れる | (++++) | + |
可能なオプションは以下の通りです。
その他仕様に関しては別途相談させていただきます。
各コーティングの硬度と酸化温度の位置付け
ALZ MSP-Q 超硬 ハイス
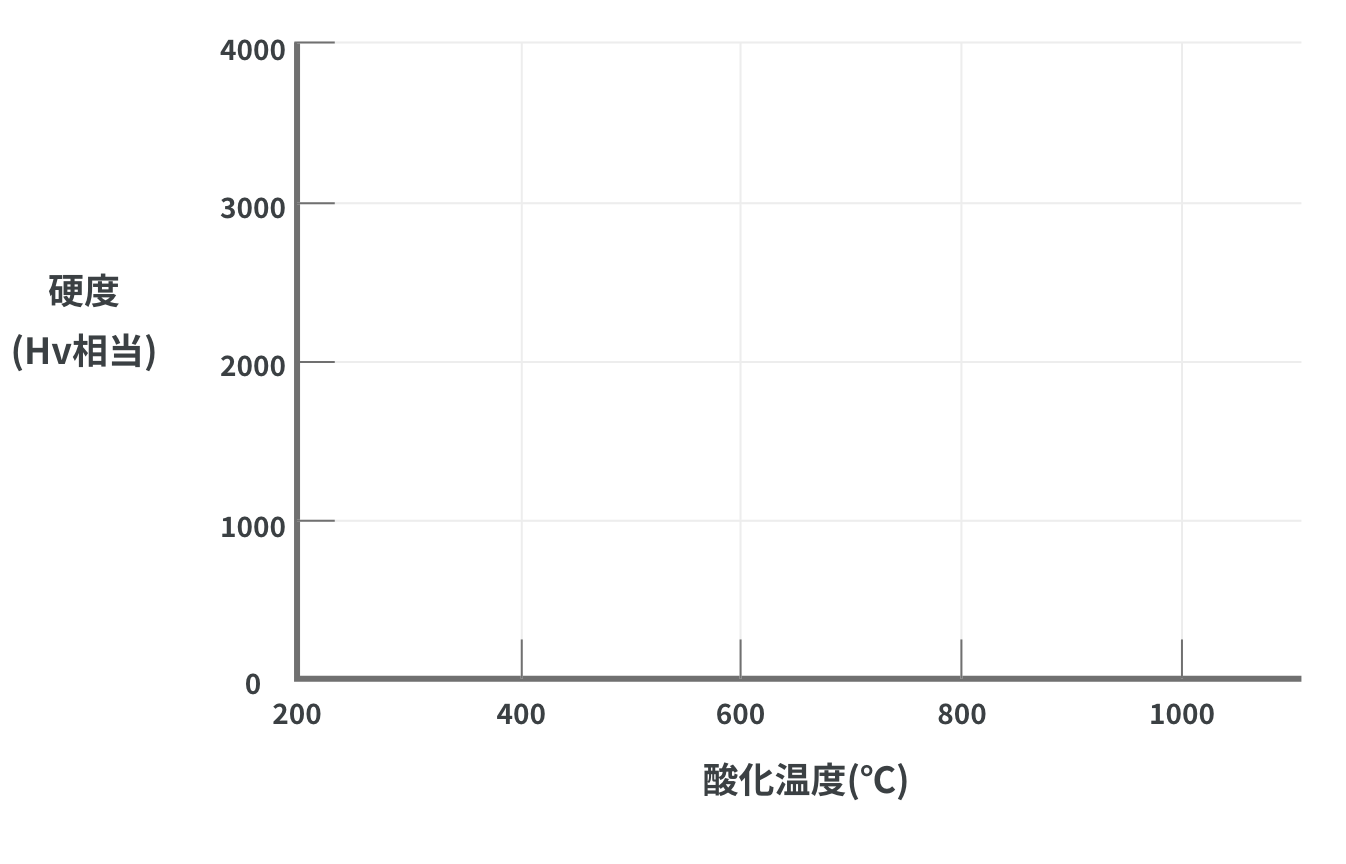
コーティング評価例
- CVD-TiCN
- ALCrN系(社外処理)
- TEST1
- TEST2
- ALM
- TCN
- ALC
- 工具
- #6ダイス側ピン
- 寿命形態
- 先端ベアリング部縦スジ摩耗
- 工程
- 抜き 板厚11mm
- ピン先端径
- Φ8.4
- ピン材質
- VM30